Fireworks shower the skies with science
A dramatic fireworks display can be the highlight of a summer. It also can provide a feast for the senses. Bright colors delight the eye. Thunderous booms and whistles surprise the ear. If you’re close to the show, you can feel the pressure waves that ripple from each exploding shell. And folks downwind of the action can smell the burnt gunpowder that fueled each rocket — and perhaps even taste it in the air.
More than 14,000 fireworks displays light the night each 4th of July, according to the American Pyrotechnics Association. (Pyrotechnics is the art of making or displaying fireworks.) But Independence Day the isn’t the only time for such shows. New Year’s Eve is also a popular time for this colorful artistry. More and more often, even small celebrations, such as graduations, are going off with a bang. And then there are all of those sporting events and rock concerts. Altogether, pyrotechnic displays throughout the United States, last year, shot off more than 8.6 million kilograms (19 million pounds) of fireworks.
These days, there’s more to putting on a fireworks show than lighting a fuse and running for cover. Things can get really complicated — and quickly.
Large shows can run for many minutes and involve thousands of shells. Many have a musical soundtrack that plays on the radio while colorful bursts light up the sky. For such shows, timing is everything. So people who design these spectacles have to make sure that each shell explodes at just the right moment. They also have to consider how a show might look from different angles and locations. Then engineers and technicians have to build the electronic circuits to control the action.
But long before a show begins, people have to design the fireworks. At what height should each shell explode? How broad should the burst be? What color — or combination of hues — should each burst deliver? Answers to these and many other questions provide show designers with the outline for the pyrotechnic displays that become true crowd-pleasers.
The evolution of fireworks
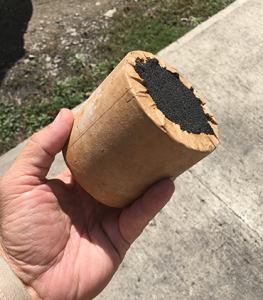
Each streak of light emanating from a fireworks burst comes from a packet of chemicals (one shown) that contains fuel, an oxidizer and the metallic powders that provide color when they vaporize. Fireworks by Grucci
Fireworks were probably invented in China more than 2,000 years ago. There, people found that when they tossed a bamboo stalk into a flame, it exploded. As air pockets in the bamboo overheated, they’d expand enough to shatter the stalk. The sudden bang would supposedly ward off evil spirits.
Centuries later, chemists added a crude type of gunpowder to these bamboo bomblets. That made the bangs bigger. Somewhere along the line, people found that adding metal powders and shavings to their mixtures made things sparkle. Later, they developed rockets by packing these materials into stiff paper tubes.
Modern-day fireworks are high-tech versions of those ancient Chinese devices. Today’s shells typically include some sort of fuel, often gunpowder. They also contain a chemical called an oxidizer. This helps the fuel burn more quickly. The shells also contain chemicals whose recipes include metals. Those metal-based compounds play a big part in determining the color of fireworks, explains Phil Grucci. He’s the owner of Fireworks by Grucci in Bellwood, N.Y. His family business has been operating for almost 170 years.
As a shell’s fuel explodes, it releases a sudden burst of heat. That energy, in turn, excites electrons orbiting metal atoms packed along with the fuel, Grucci explains. Excited electrons jump to a higher orbital. Soon, they’ll drop back to their original orbits again. At this point, the metal atoms emit a characteristic color of light.
Different chemicals produce different hues. For example, chemicals that contain barium give off a greenish light. Copper yields a blue light. This can be easily seen in an experiment that’s often a staple of high-school chemistry classes, says Grucci. A small wire is dipped into a powder and then thrust into a small flame. The color of the flame changes with the elements contained in the powder.
To come up with a new color for a firework, members of Grucci’s team, as well as the chemists they work with at other companies, do a version of that wire test. Now, however, these tests take place in bigger, better-funded labs.
Coming up with a new color can take a lot of time and involve a lot of trial and error. But by choosing and mixing chemicals in the right proportions, chemists can make a shell that will display almost any color imaginable, he notes.

And now for the physics
Fireworks displays depend on a lot of physics and engineering, notes Grucci.
On the small scale, the size and shape of particles inside a shell affect how quickly they will burn. That, in turn, affects how long a burst’s glow lights up the sky. Also, as Chinese inventors long ago noted, slow-burning gunpowder doesn’t explode. Instead, it gives off gases that can provide thrust for a rocket if they’re forced through a nozzle.
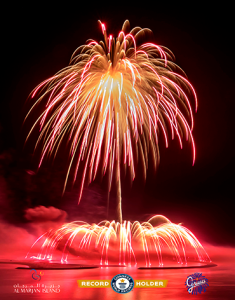
A lot of engineering went into the design of this record-breaking shell, which rose more than 1,100 meters into the sky with a burst that spanned more than a kilometer.
Fireworks by Grucci
To design a fireworks shell that rises to a certain height before it blows up, there’s a lot of math and lab work to be done. For instance: How quickly does 1 kilogram (2.2 pounds) of a particular mixture of gunpowder burn? What volume of gas does it give off? (Those things can be measured in the lab.) How much weight can that lift? (That can be measured in a field test.) Together, those data can help engineers figure out how much gunpowder will be needed to send a 10-kilogram (22-pound) shell, say, up 500 meters (1,640 feet) into the air.
On larger scales, engineering challenges can be just as daunting. Consider the world-record-size shell that Grucci’s company recently developed. The projectile measured about 1.5 meters (5 feet) across and weighed a whopping 1,000 kilograms (1.1 U.S. tons). It was fired from a tube and rose to a height of more than 1,100 meters (3,600 feet) before it burst. When the shell exploded, its colorful display measured more than 1 kilometer (0.6 mile) across.
One challenge, says Grucci, was fine-tuning the strength of the shell’s outer casing, which was made of many layers of paper. For one thing, the casing had to be strong enough to survive the launch, he notes. (When the shell left its launch tube, it was traveling at a speed of 122 meters [400 feet] per second.) But the shell’s outer casing couldn’t be too strong or the shell wouldn’t burst open properly when it reached peak height, says Grucci. The engineers used computer software to estimate how shell casings of various thicknesses might stand up to the stresses of launch and explosion. At the same time, a different team was designing the steel tube needed to launch the shell. It ended up being 7 meters (23 feet) long. Designing and building it took his teams more than 10 months.
“Designing that shell was quite an interesting journey,” says Grucci. Near the end of the process, “all our math lined up,” he notes. And the team’s lab tests suggested that the shell would work, he adds. “But at some point in time you’ve just gotta build it and launch it.”
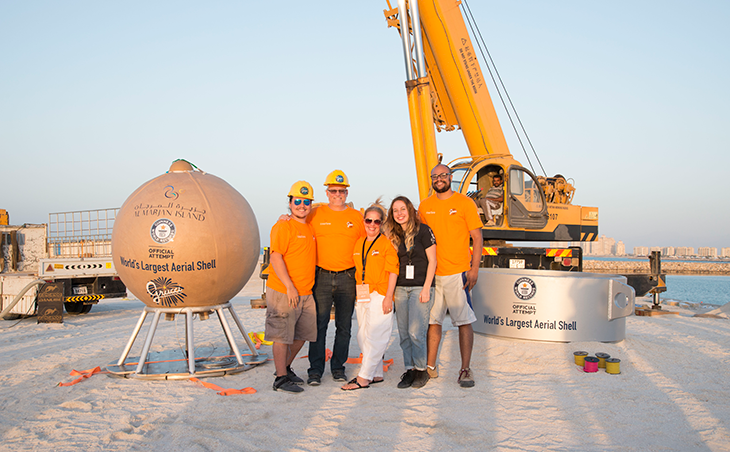
Many challenges remain to be tackled, says Grucci. He’d like to be able to reduce the amount of smoke that each shell produces. This might involve tweaking the ratio of fuel to oxidizer inside the shell. That, in turn, might lead to more complete burning of the chemicals inside the rockets. And needing smaller amounts of ingredients could greatly reduce overall costs. But there’s another reason to go smokeless, he notes. Smoke emitted by shells designed to burst at low altitude can obscure the view of fireworks exploding higher up.
Holiday fireworks can bring extreme pollution, India finds
Plus, Grucci would like to make his fireworks more ecofriendly. Smoke itself can be a problem, polluting the air. And many of today’s shell casings are no longer bamboo, but plastic. As the shells explode, they send a rain of little plastic bits falling all over the ground. “Greener” fireworks, he says, might house the rocket’s ingredients in polymers that are biodegradable. That way, the debris that falls to the ground might naturally break down over time.
Creativity reigns
A company that puts on only one or two fireworks shows per year probably wouldn’t earn much money. So it pays to diversify beyond staging shows on the 4th of July and New Year’s Eve. And many companies have done just that.
Among them is Pyrotecnico, based in New Castle, Pa. It stages some 3,000 shows across the United States each year, notes owner Stephen Vitale. The majority of those are small community celebrations. But the company also has staged events that range from a Super Bowl halftime spectacular to weddings (where, Vitale says, “Our fireworks are the icing on the cake”).
Fireworks are “obviously a visual business,” says Vitale. But shows, particularly the large ones, have really evolved in recent years. “About 50 percent of the shows we do are choreographed with a musical soundtrack,” he explains. “With music, crowds get more emotionally involved in the show.”
Making sure the soundtrack lines up with the bursting fireworks takes a lot of effort — and a lot of creativity. For each minute that a fireworks show lasts, his designers spend somewhere between 2 and 3 hours ahead of time getting the details right. They typically design the show using computer software. That software started out as an off-the-shelf program. Team members then tweaked the software to add new features. For instance, designers have to take into account how high a shell will fly, as well as how long it takes to reach that height and then burst to light the night sky.
In a sense, Vitale says, a fireworks show is like staging a play. “In the first scene, you grab the audience’s attention. After starting out strong, you program in a series of ‘Wow!’ moments,” he points out. “Then, you end with a bang!”
Designing the succession of bursts in a computer allows planners to visualize how a potential show will look. It also gives the company a way to preview the show. Designers can view via computer what the show would look like from any location in the area and from any angle. The team can then tweak the display as needed.
The opportunity to be creative attracts a lot of people to the field, says Vitale. “People get to be their own designer and choreographer, or direct their own play or movie,” he notes. It’s a very satisfying business, he adds. “We try to make a difference every day — to put a smile on people’s faces.”
Diversity pays
Pyro Spectaculars by Souza is based in Rialto, Calif. It stages shows at all scales. On the small end, they might run a show at graduations that lasts only a minute or two, says Jim Souza. He’s the company’s president and creative director. On the big end, they’ve orchestrated a 25-minute fireworks show shot from four river barges and the 580-meter-long Brooklyn Bridge in New York City. That spectacle sent up about 50,000 shells and other devices. Each year on the 4th of July alone, Souza’s company stages about 400 shows.
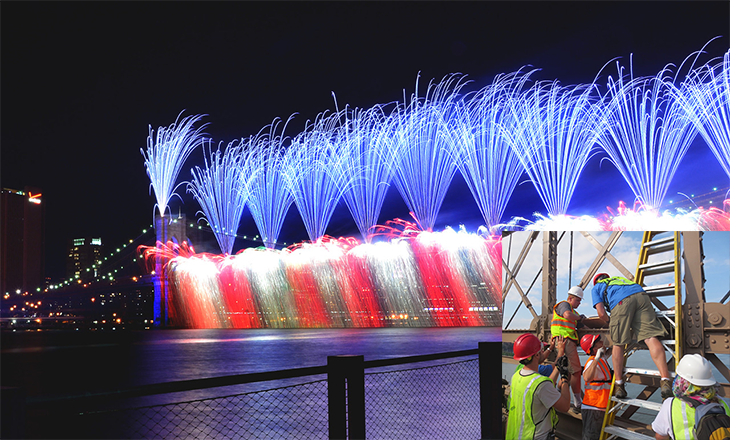
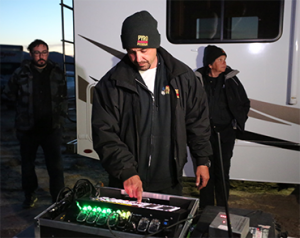
Many fireworks shows are synchronized with a musical soundtrack and are designed to start with the push of a button.
Pyro Spectaculars by Souza
When his designers put together a show, they start by creating what Souza terms “a script.” From that, they map out what sort of shells they’d like to use and how high those shells should burst. They also, among other things, decide where each shell should be fired from. In the virtual model that the designers create, events are precisely timed, Souza notes — “usually down to the tenth of a second.” They also work closely with clients to make sure that any musical soundtrack triggers “excitement, enjoyment and a lot of emotion,” he adds.
Souza has 60 full-time employees at 10 offices around the world. His teams also work with hundreds of technicians that have many different specialties. In the United States, these technicians usually are certified by local or state authorities. To be certified in California, for example, the technicians must go through a training program, take a detailed test and have two years of job experience.
Besides being trained in safety, the technicians have to be handy with tools and keenly creative. These are the workers who turn the designers’ visions into a reality. Some design and assemble the circuits that control when shells get fired. Others design and build the brackets that hold fireworks at a particular angle so that the shells will fly off and burst at the proper locations and heights. Yet other technicians may have to hang off the sides of skyscrapers and bridges to install brackets and wiring.
More than 50 people helped set up the fireworks show that lit up the Brooklyn Bridge, notes Souza. It took two weeks to set up a show that was over in less than half an hour.
Like all fireworks firms, Souza’s company has to abide by state and local environmental rules. One recent challenge has been a need to reduce their use of chemicals called perchlorates (Per-KLOR-aytes). If some of those oxidizers are left over when a shell explodes, they can drop into waterways or onto soil and affect animals and plants living or growing there. Not only that, they can be harmful to human health. Among other problems, they can reduce the production of hormones in the thyroid gland.
So, there’s plenty of challenges for people to address, both in the near term and into the future. The fireworks industry relies on many types of experts, says Grucci. In the end, one of the biggest challenges may be meeting customer expectations. To make a “seamless performance,” he says, “chemistry, engineering and artwork all have to come together.”
Learn about the chemistry of fireworks from John Conkling of Washington College in Chestertown, Md. You can trust this guy as he’s literally written the book on making fireworks (a textbook, that is).
Reactions/American Chemical Society/YouTube